Understanding OEM CNC Turning Parts Factory
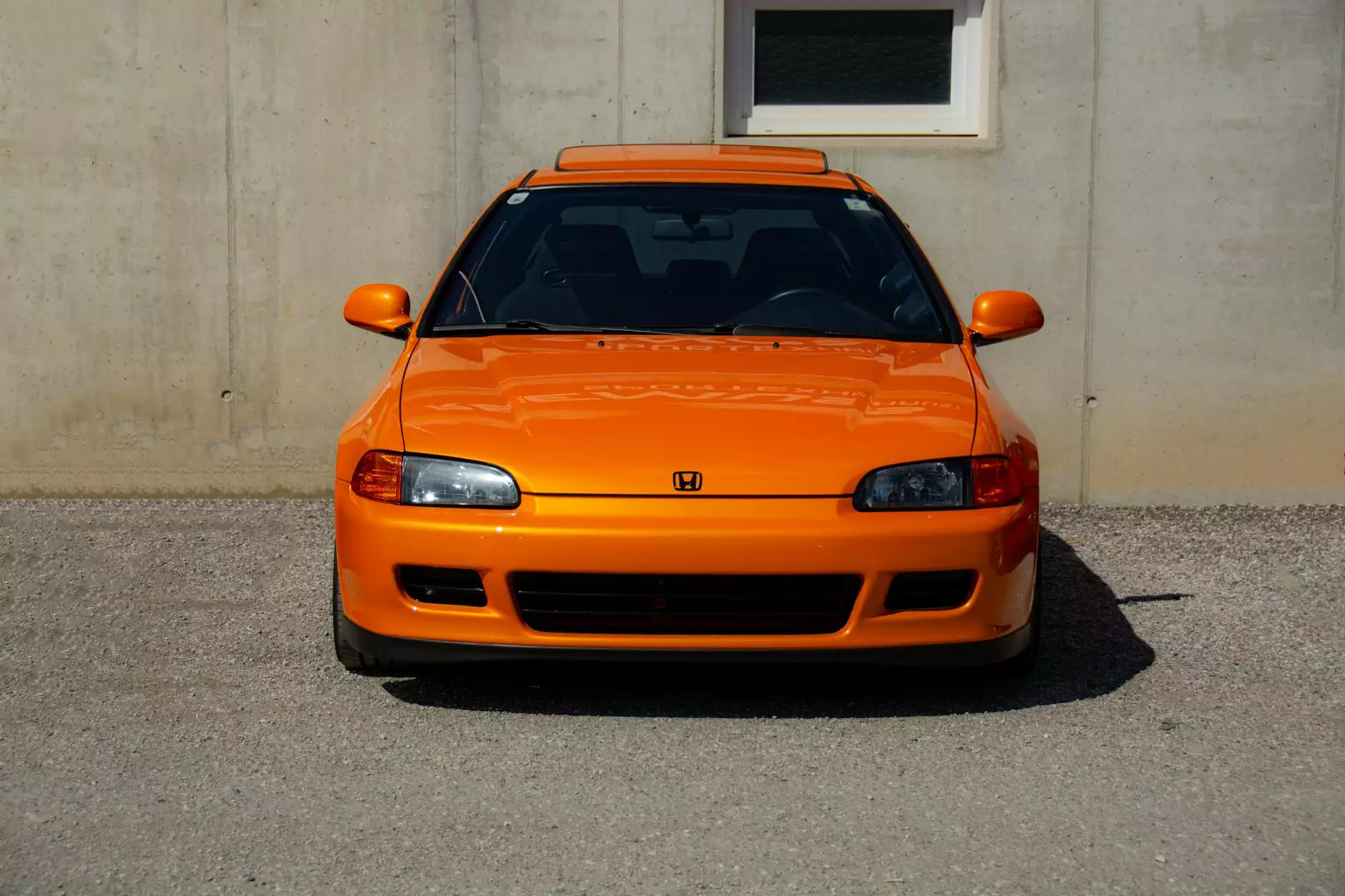
In the dynamic landscape of modern manufacturing, an OEM CNC turning parts factory plays a pivotal role in supplying industries with precision components. These factories are at the heart of metal fabrication, driving innovation and supporting a wide array of applications across various sectors such as automotive, aerospace, and electronics. This article delves into the intricacies of OEM CNC turning parts manufacturing, exploring their importance, advantages, and the technological advancements shaping their future.
What is OEM CNC Turning?
The term OEM stands for Original Equipment Manufacturer. In the context of CNC turning, it involves producing parts that meet specific requirements outlined by another company, ensuring that these components fit seamlessly into the intended products. CNC turning itself is a subtractive manufacturing process that utilizes computer numerical control technology to shape materials into desired forms through the rotation of a workpiece against a cutting tool.
The Process of CNC Turning
Understanding the process that takes place within an OEM CNC turning parts factory is fundamental. The CNC turning process encompasses several key steps:
- Design and Prototyping: It begins with a detailed design phase where the specifications of the parts are established. This often includes creating 3D models and prototypes to ensure accuracy.
- Material Selection: Factories often use various materials such as aluminum, stainless steel, and other alloys depending on the part's application and required properties.
- Programming: The CNC machine is programmed with precise instructions derived from the computer-aided design (CAD) files.
- Turning Process: A turning machine (lathe) rotates the workpiece while a cutting tool removes material, creating the desired shape and dimensions.
- Quality Control: Once the parts are manufactured, rigorous quality control measures are implemented to ensure that each part meets the established specifications.
Advantages of OEM CNC Turning Parts Manufacturing
The advantages of utilizing an OEM CNC turning parts factory are manifold, ranging from precision manufacturing to efficiency in production. Here are some of the key benefits:
- High Precision: CNC machines offer unmatched precision, allowing for the creation of complex geometries and intricate designs that would be challenging to achieve with manual machining.
- Scalability: OEM CNC turning parts factories can efficiently scale production up or down, making it easier to meet fluctuating demands in various industries.
- Cost-Effectiveness: Although the initial investment in CNC technology can be significant, the long-term cost savings through reduced labor, minimal waste, and fewer errors make it a financially sound choice.
- Versatility: These factories can produce a wide range of parts for different applications, from simple components to highly complex assemblies.
- Consistency: Once a CNC program is established, it can reproduce parts consistently, which is crucial for maintaining quality across large production runs.
The Role of Technology in CNC Turning
In today’s fast-paced manufacturing environment, technology plays a critical role in the efficiency and effectiveness of operations within an OEM CNC turning parts factory. Here are some advancements that have significantly impacted CNC turning:
Automation
Automation technology has transformed CNC turning operations by introducing robotic arms and automated loaders, which can handle material input and out, significantly increasing production speed and efficiency. This minimizes human error and maximizes throughput.
Advanced Software Solutions
Modern machining relies heavily on advanced software solutions for design and production monitoring. CAD/CAM software allows for rapid design modifications and process optimizations, streamlining the workflow from concept to finished product.
Real-Time Monitoring
Using the Internet of Things (IoT), manufacturers can now implement real-time monitoring systems. These systems provide valuable data insights regarding machine performance and production statistics, enabling quick decision-making to address any potential issues that may arise during the production process.
Quality Assurance in CNC Turning
Quality assurance is a cornerstone of operations within an OEM CNC turning parts factory. Manufacturers implement several strategies to ensure that only the highest quality parts are produced:
- Inspection Protocols: Regular inspections during the production process using precision measuring tools like calipers and gauges to ensure that parts meet specifications.
- Certification Standards: Adhering to international quality standards such as ISO 9001, which ensures that manufacturing processes are consistent and standardized.
- Feedback Loops: Establishing feedback mechanisms that involve all stakeholders in the production process, allowing for continuous improvements based on performance data.
Applications of CNC Turning Parts
OEM CNC turning parts are utilized in various industries, catering to an array of applications. Here are some notable examples:
Automotive Industry
The automotive sector is one of the largest consumers of CNC-turned components. Parts such as engine blocks, shafts, and fittings are manufactured with precision, contributing to vehicle performance and safety.
Aerospace Sector
In aerospace applications, precision is paramount. CNC turning factories produce critical components such as turbine blades and landing gear parts, where even the slightest error can have catastrophic consequences.
Medical Equipment
The medical field requires high-quality, sterile components. CNC manufacturing plays a crucial role in creating precise instruments and devices used in surgical procedures and diagnostics.
The Future of OEM CNC Turning Parts Factories
Looking ahead, the future of OEM CNC turning parts factories is likely to be shaped by several trends:
- Increased Personalization: As consumers demand more personalized products, CNC turning technology will evolve to produce one-off designs efficiently.
- Sustainability Practices: Emphasizing eco-friendly practices will become imperative, leading factories to implement greener processes and materials.
- Integration of AI and Machine Learning: Factories will increasingly rely on artificial intelligence for predictive maintenance, quality control, and production planning.
Conclusion
In summary, an OEM CNC turning parts factory is a crucial player in the realm of metal fabrication, providing essential components for various industries. With its ability to deliver high precision, scalability, and cost-effectiveness, CNC turning technology continues to innovate and set benchmarks for quality. As manufacturing evolves, these factories will remain at the forefront, integrating advanced technologies and practices aimed at fulfilling the ever-growing demands of the market.
As businesses seek reliable and precise manufacturing partners, understanding the value and capabilities of OEM CNC turning parts factories becomes increasingly important. At deepmould.net, we are committed to providing high-quality machining solutions tailored to meet the unique needs of our clients across various sectors. Engage with us and discover how we can elevate your manufacturing processes today!