The Critical Role of Lathe Parts Manufacturers in Precision Engineering
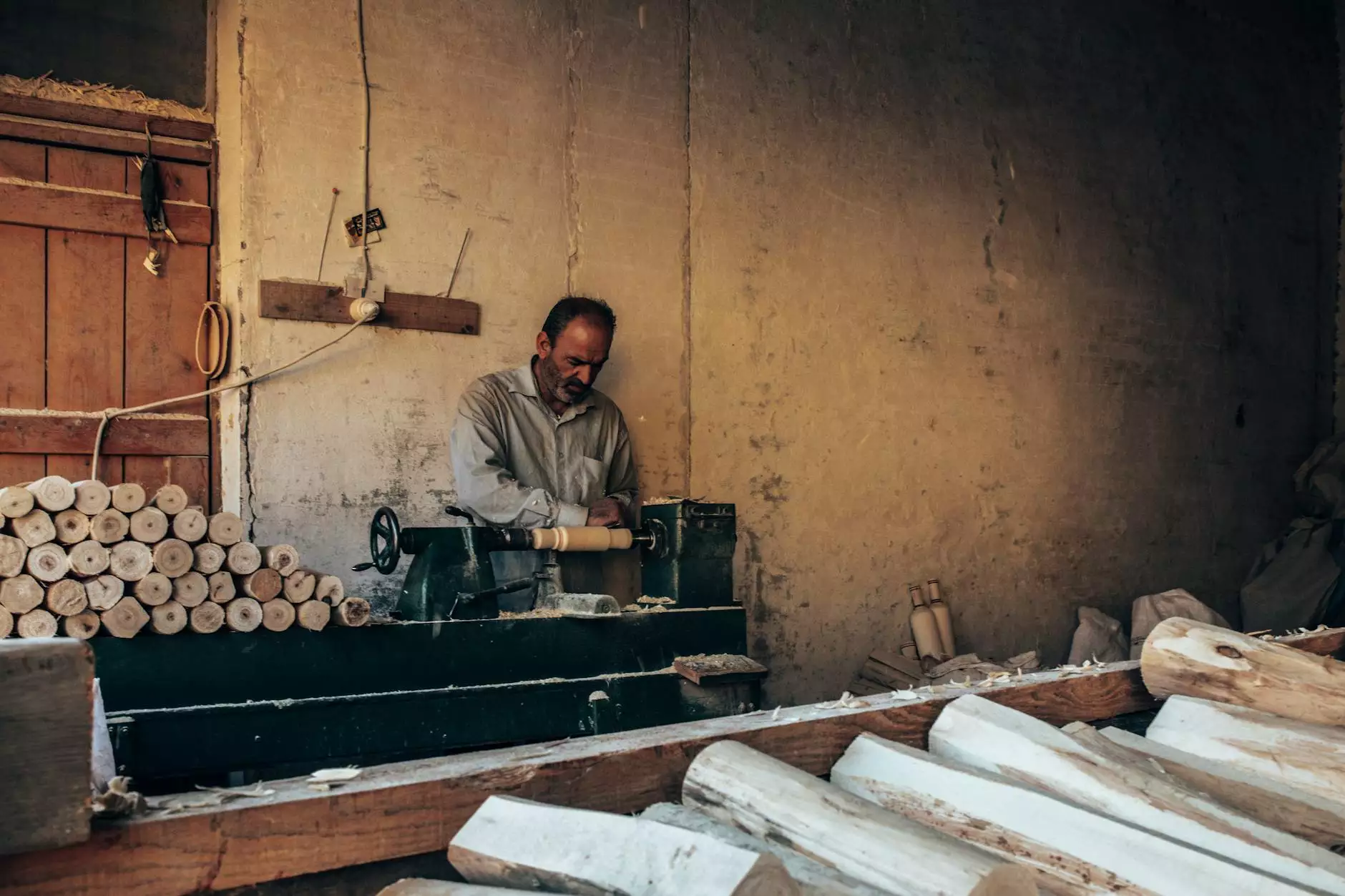
In the vast and intricate world of manufacturing, few processes are as essential as those performed by lathe parts manufacturers. These skilled artisans and engineers play a pivotal role in the production of precision components that are the backbone of countless industries. From automotive to aerospace, the parts produced on lathes are vital for the functionality and reliability of many products we use daily.
What Are Lathe Parts and Why Are They Important?
Lathe parts are components manufactured using lathe machines, which are used to shape materials—typically metals and plastics—by rotating the workpiece against a set cutting tool. The precision achieved through this manufacturing method is unparalleled and is essential in producing items that require exact measurements and fine tolerances.
The importance of lathe parts extends across various sectors, making the role of lathe parts manufacturers fundamental in ensuring that these industries function smoothly and efficiently. Here are a few reasons why lathe parts are crucial:
- Precision Engineering: Lathe parts are crafted to meet exact specifications, ensuring the highest level of accuracy in final products.
- Durability: Components made with lathe processes often exhibit superior strength and wear-resistance, crucial for demanding applications.
- Versatility: If there's a need for custom shapes or complex features, lathe manufacturing can easily adjust to create various parts rapidly.
- Cost-Effectiveness: Large quantities of parts can be produced efficiently, making it a viable option for mass production.
How Are Lathe Parts Manufactured?
The manufacturing process involves several steps, each critical to ensuring the quality of the final product. Let’s explore this intricate procedure:
1. Design and Specification
The first step involves designing the part using Computer-Aided Design (CAD) software. Engineers provide detailed specifications, including dimensions, material types, and finish requirements, which guide the subsequent manufacturing stages.
2. Material Selection
Choosing the right material is essential in lathe manufacturing. Suppliers often provide a range of metals and plastics, each with unique properties. High-carbon steels, stainless steels, and aluminum alloys are popular choices due to their excellent machinability and strength.
3. Setup
The lathe machine is prepared by installing the necessary tooling specific to the component design. This ensures that the machine is ready to produce the required tolerances.
4. Machining
During the machining process, the workpiece is mounted on the lathe, which spins it while cutting tools shape it precisely. This process can involve several operations such as turning, facing, and boring.
5. Quality Control
After machining, parts undergo stringent quality control checks. Measurements are taken using precision tools to ensure they meet the required specifications. Any parts that do not meet the essential tolerances are rejected or reworked.
6. Finishing
The finishing stage may include processes such as polishing, anodizing, or coating to improve the appearance and functionality of the lathe parts. Finishing is crucial for parts used in aesthetic applications or in environments prone to corrosion.
Finding the Right Lathe Parts Manufacturer
Selecting a reliable lathe parts manufacturer is paramount for businesses requiring precision components. Here are key factors to consider when choosing a manufacturer:
1. Experience and Expertise
Opt for a manufacturer with a wealth of experience in the industry. A seasoned manufacturer will have a proven track record of producing quality parts and can provide insights that newer manufacturers may lack.
2. Technological Capabilities
The latest technology in machining often leads to higher precision and efficiency. Investigate whether the manufacturer uses advanced machinery and software to enhance their production capabilities.
3. Certifications and Standards
Look for manufacturers that adhere to relevant industry standards and hold certifications such as ISO 9001. This is an indicator of their commitment to quality management.
4. Portfolio and References
Reviewing past projects and obtaining references can provide assurance regarding the manufacturer’s capabilities. It's essential to partner with manufacturers who have successfully delivered projects similar to yours.
5. Customer Service
Effective communication and support are vital for a successful partnership. A manufacturer that prioritizes customer service will be more accessible and responsive to your needs, ensuring a smoother collaboration.
The Future of Lathe Parts Manufacturing
As technology continues to evolve, the landscape of lathe parts manufacturing is also changing. Innovations such as additive manufacturing and smart machining are gaining traction, allowing manufacturers to push the boundaries of what’s possible.
Furthermore, the integration of Industry 4.0 principles, including the Internet of Things (IoT) and automation, will likely lead to enhanced efficiency, reduced lead times, and lower production costs. Staying informed about these trends is crucial for businesses looking to leverage the latest advancements in manufacturing technology.
Conclusion
In conclusion, lathe parts manufacturers are integral to the realm of precision engineering and metal fabrication. They not only provide high-quality, custom parts but also contribute to the innovation and advancement within various industries. By understanding the significance of their role and how to select the right manufacturing partner, businesses can achieve greater efficiency and success in their operations. For more detailed inquiries or to explore your options in high-quality lathe parts, visit deepmould.net.