Understanding Precision CNC Machining: The Key to Quality Metal Fabrication
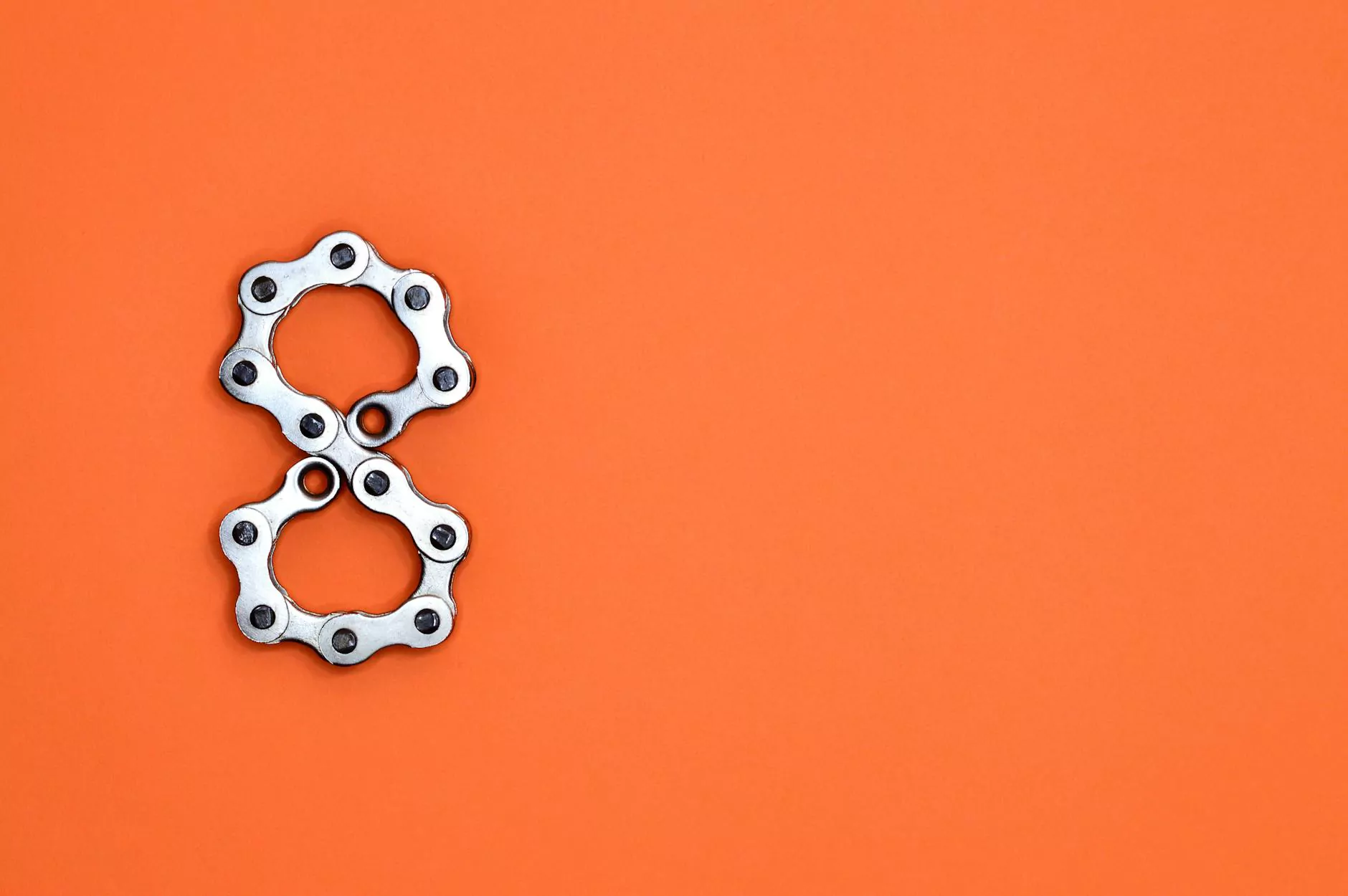
In the competitive world of manufacturing, precision is paramount. For businesses looking to achieve the highest standards in metal fabrication, a precision CNC machining company like DeepMould stands out as an essential partner. This article delves into what precision CNC machining is, its advantages, and why choosing a top-notch machining company can elevate your production capabilities.
What is Precision CNC Machining?
CNC, or Computer Numerical Control, machining refers to the automated process of using computer software to control machine tools. This method allows for the creation of intricate parts with remarkable accuracy and repeatability. In a precision CNC machining company, the term “precision” highlights the ability to manufacture components within extremely tight tolerances, ensuring that every piece meets exact specifications.
The Machinery Behind Precision CNC Machining
At the heart of this machining process are advanced machines equipped with sophisticated controls. Some of the most commonly used machines include:
- CNC Lathes: Ideal for symmetrical parts, CNC lathes rotate the material while a cutting tool is fed into it.
- CNC Mills: These machines remove material from a workpiece to shape the desired component, often through milling, drilling, and tapping.
- CNC Routers: Typically used for softer materials like wood, plastic, and foam, CNC routers perform similar functions to CNC mills.
- Wire EDM Machines: Electrical discharge machines use electric sparks to shape materials and are incredibly effective for precise cutting.
The Advantages of Using a Precision CNC Machining Company
Choosing a precision CNC machining company like DeepMould comes with numerous advantages for your manufacturing processes. Here are some notable benefits:
1. Unmatched Precision and Accuracy
The hallmark of precision CNC machining is the ability to produce parts with impeccable accuracy. Tolerances as tight as ±0.001 inches are achievable, ensuring that every component fits perfectly within an assembly. This precision reduces assembly time and can lead to a decrease in product defects.
2. Increased Efficiency and Production Speed
Automation plays a vital role in enhancing production speeds. CNC machines can operate continuously, allowing manufacturers to produce large volumes of parts without compromising quality. This efficiency translates into quicker lead times, helping businesses respond faster to market demands.
3. Cost-Effectiveness
While the initial investment in precision CNC machining may be higher, the long-term savings are significant. By minimizing waste through accurate cuts and reducing the need for extensive manual labor, businesses can lower production costs. Additionally, high-quality output decreases the likelihood of rework, further saving resources.
4. Versatility Across Industries
One of the remarkable facets of precision CNC machining is its versatility. It can be utilized in various sectors, including:
- Aerospace: For components that must withstand extreme conditions.
- Automotive: For producing intricate parts that require durability and precision.
- Medical: In the manufacturing of precision instruments and customized implants.
- Electronics: For producing components that require exact specifications.
Precision CNC Machining Process Explained
Understanding the process flow in a precision CNC machining company such as DeepMould is crucial for appreciating how high-quality parts are produced. Below, we outline the key stages:
1. Design Phase
The first step involves creating a detailed design of the part. Engineers typically use CAD (Computer-Aided Design) software to develop precise models that reflect all necessary specifications. These designs will be key in programming the CNC machines.
2. Programming the CNC Machine
Once the design is finalized, it is translated into G-code, which is the language CNC machines understand. This programming defines every movement the machine will make, including cutting paths and speeds.
3. Material Selection
Choosing the right material is fundamental in precision CNC machining. Common materials include aluminum, steel, brass, and plastics. The selected material must meet the specific requirements of the intended application, whether they involve strength, weight, or thermal characteristics.
4. Machining Operations
During this stage, the actual machining occurs. The CNC machine uses the programmed instructions to cut and shape the raw material into the predefined design. Continuous monitoring ensures that the process stays on track.
5. Quality Control
To guarantee that each part meets the necessary standards, rigorous quality control checks are implemented. Measurements are taken, and dimensions are verified using precision tools such as calipers and CMMs (Coordinate Measuring Machines).
6. Finishing Touches
After the primary machining process, finishing processes such as deburring, polishing, or coating may be applied to enhance the aesthetics and functionality of the part.
Trends in Precision CNC Machining
The field of CNC machining is dynamic, with continual advancements reshaping how precision parts are manufactured. Some significant trends include:
1. Automation and IoT Integration
The Internet of Things (IoT) is revolutionizing manufacturing by enabling machines to communicate with each other. This integration enhances operational efficiency and predictive maintenance, minimizing downtime.
2. Advanced Materials
As technology advances, new materials, including composites and advanced alloys, are being utilized in CNC machining, enabling the production of lighter but stronger components.
3. Sustainability Initiatives
Many precision CNC machining companies are embracing sustainable practices, including waste reduction measures and the use of recyclable materials, aligning with the growing demand for environmentally-friendly production methods.
4. 3D Printing Convergence
3D printing and CNC machining are converging to offer hybrid solutions. This collaboration allows for the rapid prototyping of parts before full-scale CNC machining, streamlining the development process.
Choosing the Right Precision CNC Machining Company
With numerous options available, selecting the right precision CNC machining company can be daunting. Here are critical factors to consider when making your choice:
1. Experience and Expertise
Look for a company with extensive experience in CNC machining and a proven track record in your industry. Expertise ensures they can handle complex projects and deliver high-quality results.
2. Technology and Equipment
Advanced technology leads to better precision and efficiency. Ensure that the machining company utilizes state-of-the-art equipment and stays updated with technological innovations.
3. Quality Control Measures
Investigate the company's quality control processes. A robust quality assurance program indicates that they prioritize producing defect-free products.
4. Customer Reviews and Testimonials
Customer feedback can provide insight into the company’s reputation and the quality of their service. Look for testimonials that highlight their strengths and reliability.
5. Cost Competitiveness
While price shouldn't be the only deciding factor, it is important to choose a company that offers competitive pricing without compromising on quality.
Conclusion: The Future of Precision CNC Machining
In conclusion, the role of a precision CNC machining company like DeepMould is pivotal in today’s manufacturing landscape. As industries continue to evolve and demand higher quality and precision, the capabilities offered by CNC machining companies will remain invaluable. Investing in precision CNC machining not only enhances the quality of your products but also contributes to overall operational efficiency, enabling your business to stay ahead in a competitive marketplace.
By choosing a trusted partner in manufacturing, like DeepMould, you ensure that your production goals are met with precision, speed, and reliability. Ready to elevate your metal fabrication processes? Contact us today!